New Research Brings Beam Structures to Generative Design
Have you ever wished that your generative designs were less organic and easier to build from parts you can pick off the shelf? What if you could automatically generate structures from standard beams that you can weld together in your shop to fit your problem scale and configuration?
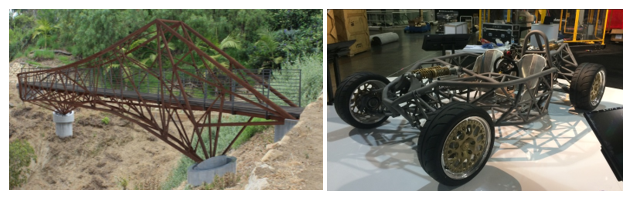
Real-world structures built from welded beams
Our team developed a new form of generative design that helps users to create structures that are easy to fabricate on a shop floor. Instead of generating bone-like or organic structures that can only be 3D printed and are challenging to create at scale, this new tool lets you create large frame designs that you can build by welding together a set of tube or beam extrusions. It even helps you to simplify the joints and align the beams, while keeping the structure rigid and supporting the required loading. This new approach offers much of the advantage for an optimized design, but without the cost and duration of 3D printing.
Autodesk introduced generative design for manufacturing at Autodesk University 2014, showcasing early research prototypes which later became the generative design tools available in Fusion 360 today. These initial tools allowed users a new level of automation for design. Instead of drawing the geometry using CAD tools to satisfy the problem requirements, the user would inform the system of the constraints and requirements and, using an iterative optimization approach, the system would generate the new geometry options. These geometry types were initially generated by tools that made use of physics simulation to determine optimal structures with no specific limitation on shape or manufacturability. Since the physics for optimization explored a free-form approach, the resulting shapes strongly resembled biological structures, such as tree limbs or bones. These designs are highly curved and complex.
The assumption was that 3D printing would come to the rescue and manufacture whatever we designed. Then, we could take full advantage of the physical optimality. In certain cases that was true, and we managed to replace human designs with much lighter and stiffer 3D printed components. However, 3D printing is not the silver bullet that can solve all manufacturing challenges. We still must struggle with large scale production and limitations in the size of the print volume. With this in mind, the Autodesk Research team explored a variety of manufacturability constraints with generative design to support milling and casting, along with improved support for 3D print manufacturing methods.
However, there is still a gap. A common manufacturing approach is to combine a set of extrusions, either tubes or beams at joints, to form frame structures such as a vehicle chassis, stage supports, or countless other designs. This is a practical, lightweight, speedy, and relatively cheap method used all over the world. Because it relies on a combination of standard parts, the designer can scale up to solve problems of any size. While it is true that standard topology optimization does give results that appear beam-like, when closely examined, the final geometry is subtly quite different and extracting regular beams from it is a significant manual undertaking. Our new tool was created to save you the time, effort and expense, while offering designs optimized for this manufacturing method.
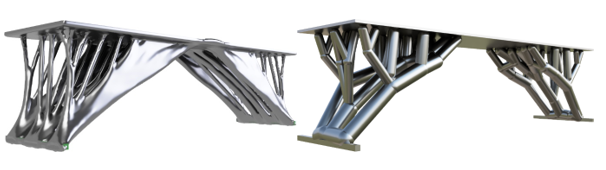
Footbridge designs with standard generative design (left) and with beam optimization (right)
Our goal was to allow generative design users to keep the common tools we have developed while also enabling the design of beam structures. Our new method offers users the same configuration setup where load cases are defined and materials are chosen, but with the option to turn on the new beam manufacturability method with a few additional parameters. Importantly, the designer does not need to specify special geometry. The user doesn’t need to know how many beams the final design will require nor where they need to be placed. Instead, the system takes in the preserve geometry along with loadings and gradually converges until it has determined a network of beams that smoothly connects to the preserve geometry and can support the given loads. All the user needs to specify is what material it should be and what the sizing limits should be. On top of that, the system performs snapping that creates more natural T-junctions and snaps angles between beam pairs to closely match a user-specified angle range, e.g., 45 or 90 degrees for instance. These help to create more regular frames that are easier to manufacture and assemble.
Optimization of pylon structure without angle snapping (left) and with angle snapping (right)
So how does that gradual convergence work? Under the hood, we are using topology optimization but with a special dual geometry representation. We have the smooth freeform geometry that we are familiar with from current generative design, but we introduce a second ‘idealized’ representation that includes the preserves and the connected beam elements. We offer a method of extracting the configuration of beams from the smooth geometry by tracing center lines or ‘skeletons’ of that geometry and fitting beams through them. The system begins the optimization using the standard freeform geometry because the initial beam configuration is unknown. Periodically, the system extracts the beam configuration from the freeform geometry. The further that the optimization proceeds, the better that beam configuration becomes. We also have a constraint that gradually forces the freeform geometry to match up with the beam configuration. Over time, both representations converge to match each other and produce a cleanly connected beam frame structure. Then we can use the beam configuration to directly generate CAD structures instead of going through a complex mesh to CAD procedure.
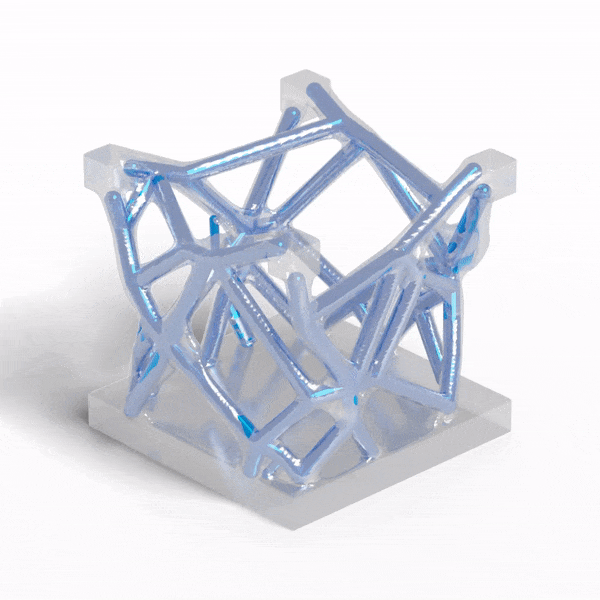
This torque resistant structure was designed with our beam manufacturability method. The freeform structure is transparent, and the beam representation is in blue, and the two representations gradually converge to match each other.
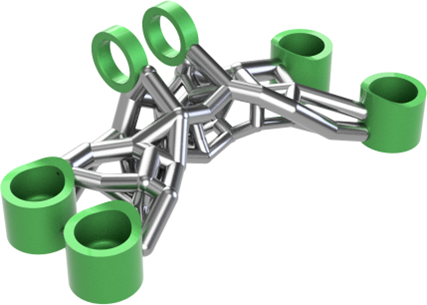
If we apply beam manufacturability on the GE bracket, we can create a beam lattice structure
It is exciting to design beam structures with such simplicity, though many real-world structures have more complexity to their cross-sections and their joints. They may require gussets and reinforcing plates to provide additional strength between two neighboring beams. The good news is that adding such functionality is straightforward with this new technique, the gusset plates can be fit to the freeform geometry at the joints in the same way that beams are fit, and the same convergence would ensue. In fact, any idealized geometry that we would like to constrain the optimization to, could be fit and set as a target, making this new technique very powerful with numerous future uses, from sheet metal stamping to fluid pipe design.
Nigel Morris is Senior Manager, Principal Research Scientist at Autodesk.
Get in touch
Have we piqued your interest? Get in touch if you’d like to learn more about Autodesk Research, our projects, people, and potential collaboration opportunities
Contact us