Exploring Carbon-Negative Materials: Autodesk Research’s Path to Net-Zero Buildings Part 2
Leading by Example at Autodesk University
Completed net-zero carbon façade installed on a full-size housing unit and exhibited at Autodesk University. This unit is one of more than 300 similar apartments that make up The Phoenix.
- Scaling up materials research for real-world application: Autodesk, in collaboration with industry partners, scaled up the production of a high-strength mycelium composite for The Phoenix, demonstrating a tangible decarbonization solution for buildings.
- Building trust with customers at Autodesk University (AU): The mycelium facade exhibited at AU inspired attendees and industry leaders, highlighting Autodesk’s leadership in sustainable materials and the industry’s readiness to adopt carbon-negative solutions.
- Data as a key component for future materials workflow: Design tools need accessible, validated material data that allows for real-time analysis and informed material choices, providing stakeholders with a unified data experience and enhancing sustainable construction outcomes. The envisioned future for material workflows is to empower designers to generate materials dynamically based on performance, aesthetic, financial, or sustainability goals, similar to how they currently think of 3D geometry.
In a recent blog post, we discussed the material breakthrough of sample 65 that began in a petri dish. As a research team, we didn’t want our work in the to end there, relegated to promising, yet unfulfilled “what-if” findings. Rather, the hurdles of making this research real and expanding it to the scale of buildings demonstrate Autodesk’s commitment to moving the needle on decarbonization today.
Working together with industry collaborators, the high strength mycelium composite core production would be scaled up and made ready for real-world use. Ecovative, a pioneer in mycelium materials, would develop a modified version of the prototype material and supply the cores. Kreysler and Associates, an innovator in advanced composites for AEC, would integrate the new bio-based cores as a drop-in solution for the novel net-zero FRP façade. Factory OS, a leader in volumetric modular buildings, would then install the façade system onto its modules in the factory before making its way out into the world. Close coordination with industry collaborators was key to ensuring that this new carbon-storing material could be demonstrated as a tangible solution for reducing the embodied carbon of buildings.
But before this facade panel found a permanent home cladding an affordable housing project in Oakland, it took a slight detour to a Las Vegas exhibition hall at Autodesk University (AU). Placed at the Expo entrance, attendees saw this groundbreaking new material in use, sensed the scale and weight of the demonstrator, and ultimately learned about—and were inspired by—how material innovations can promote a net-zero future. And, of course, they asked us questions…
“We’re interested in incorporating net-zero facades for our university projects but blocked by a lack of knowledge of tested, durable techniques that expand our low carbon material options,” said Mark Goldman, Chairman of the Green Technology Program, University of New Mexico-Taos Construction Technology Department, upon first viewing. “But is what you’re showing here real, and can we get it now?”
This was a popular sentiment repeated by industry leaders over the course of the exhibition, which was surprising in some ways. This radical new facade wasn’t met with skepticism or challenging statements, but rather a general positive response, a buzzing excitement about innovative, carbon-negative materials, and an eagerness to experience the future.
If the question posed by Autodesk University was, are you ready for what’s next? The answer from our customers was a resounding yes.
Similarly, Arthur Harsuvanakit, principal research scientist, Autodesk Research, led an AU class on the future of bio-based materials, where he met with Mike Stenson, project director at Kingspan, a global leader in advanced building envelope solutions. Mike’s enthusiasm about the material research demonstration was understandable, given that his team at Kingspan is working to develop low-carbon alternatives to traditional materials.
“It’s great to see Autodesk leading the development of new materials like the mycelium composite into industry through rigorous testing and development,” he said. “We view the advent of these material systems on display here as a necessary future for architecture and construction.”
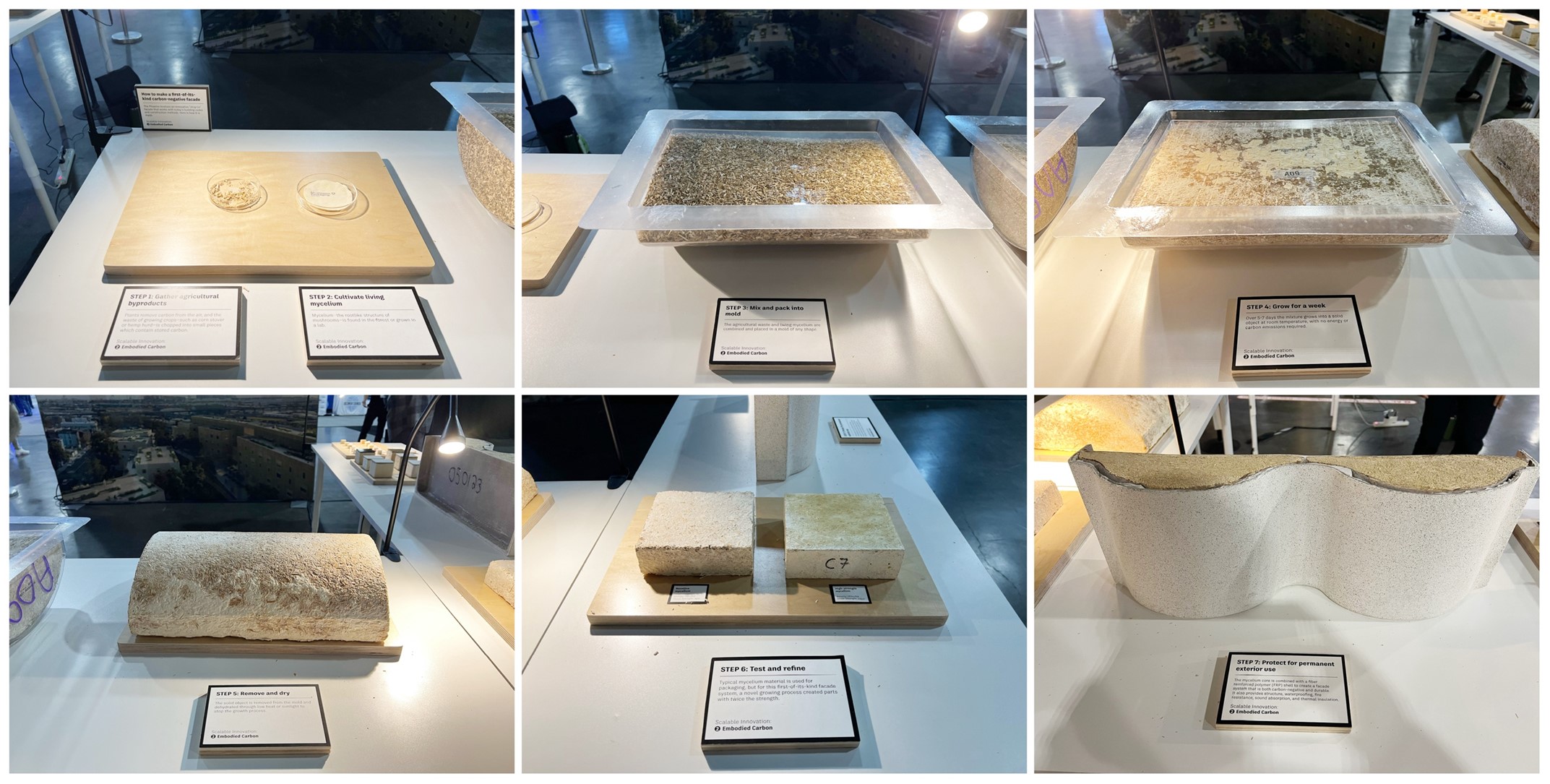
The Phoenix exhibit at AU included detailed material samples. These demonstrated to customers the overall prototyping process through informative, hands-on physical samples.
Also at AU, Rama Dunayevich, Senior Manager, Global Impact Partnerships, Autodesk hosted the Sustainability Leaders Summit (SLS), a bespoke curated experience for 18 senior sustainability executives from enterprise to start-ups and across industries. She led the SLS through a number of sustainability-focused events, the capstone of which included a luncheon at the facade exhibit. Rama described the research as “demonstrating a real-world application of new materials like mycelium, the power of radical collaboration, generative AEC, affordable housing, applied research into net zero, industrialized construction . . . [and] a true shining example of an idealized future that squarely positions Autodesk as an innovator leading the industry forward.”
Why is Autodesk, a company known for its design software, exploring materials research? Some variation of this question was a common refrain posed by customers as they explored the exhibit. In many ways, the answer is simple: Autodesk is a leader in the Design and Make Platform space. We envision materials as more than just the physical building blocks of how things are made. We know materials science properties hold powerful data that has the capacity to radically transform the amount of carbon emitted by virtually everything that is made in the future. Autodesk Research can help generate this crucial data and bring traditionally siloed stakeholders together for a common data experience.
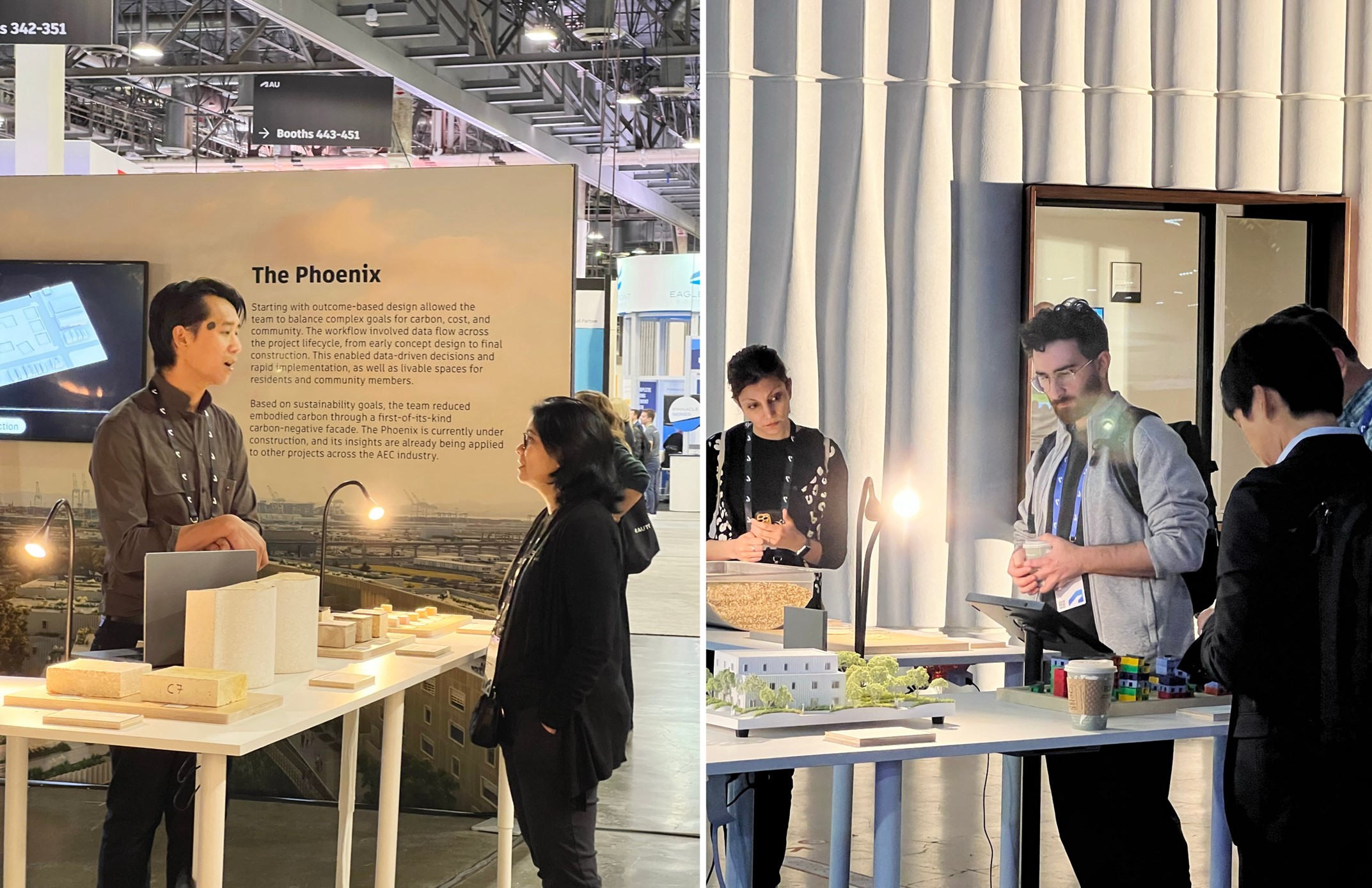
(left) Autodesk Researcher Arthur Harsuvanakit shares the carbon storing material process with an Autodesk University 2023 attendee. (right) Autodesk customers engage with the interactive exhibit materials outside of the full-scale facade prototype.
Research-to-software transfer
“At the heart of Fusion is data.”
—Jeff Kinder, Executive Vice President, Product Development and Manufacturing Solutions at Autodesk University 2023
Data connects Autodesk software to real-world materials. While Autodesk customers are ready to design sustainable projects with novel materials, there is, unfortunately, a significant gap in the availability of data, preventing the widespread adoption of low embodied carbon bio-based material. To address this disparity, material data must be (1) easily accessible, (2) third-party validated, and most importantly, (3) able to predict performance within unique conditions. That’s where Autodesk Research’s experiments with new sustainable materials comes in. Working hand in hand with our industry partners, we can “scale up” these material innovations to create widespread impact to move the needle on decarbonization.
Readily accessible data
Designing buildings with new low-carbon materials is a complex endeavor, beyond simply comparing product EPDs, as there are numerous performance criteria for each material that must be simultaneously met. Currently, existing design tools require significant detail to render results and analysis—often at a time when many material decisions have already been made. Designing a building is a fast and fluid process that can’t be held back by lack of information or bogged down by complicated carbon accounting.
The next generation of AEC tools, including Autodesk core and partner solutions for carbon analysis, such as Autodesk Insight and the Tally Climate Action Tool (tallyCAT), will allow for better material decisions to be made earlier in the design process, reducing embodied carbon by providing the designer with an environment in which reliable and updated material data is at the ready, and real-time feedback and analysis is at hand—easily accessible and seen as a constant companion.
This carbon-negative facade panel serves as an example of how these vital decisions can be made in tandem with design development progress—and demonstrates how Autodesk’s future workflows provide real-time trade-offs between carbon, cost, and livability.
Third-party validation
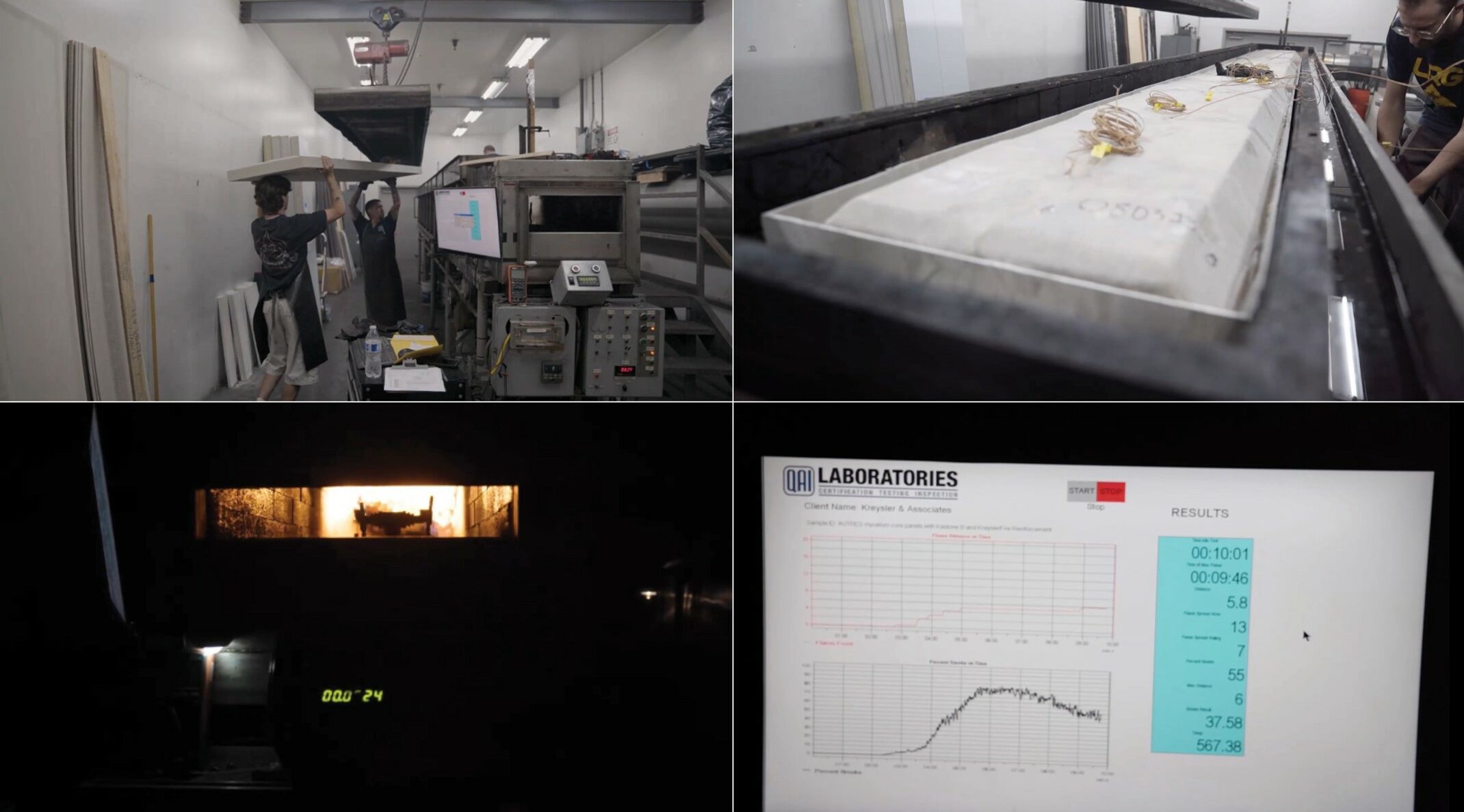
Lab technicians setting up and documenting a full scale E84 test to determine the fire rating of the bioFRP facade panel. The test specimen is 24ft long and is subjected to 10 minutes of flame exposure, measuring burning characteristics like flame spread and smoke development. The result of this test was a Class A rating—the highest level and the first ever for this type of material.
Material performance and environmental impact claims must be validated by third-party agencies. The cradle-to-cradle assessment for this façade was performed by a sustainability analysis agency, and the results will be published in a Life Cycle Assessment, following ISO 14040/14044 LCA standards and ISO 21930 towards the goal of publishing an Environmental Product Declaration (EPD). That standardized EPD will provide the foundational data for future Autodesk Fusion and Autodesk Forma users to design with this same mycelium facade system in their own projects—confident in the accuracy of the structural simulation performance and environmental impact data, which includes embodied carbon.
EPDs are not only an important tool for data transparency, but they also provide a framework for enabling future generalizable workflows. Autodesk Research closed the loop on materials research by successfully generating data through an iterative process of physical materials testing and incorporating that data into a replicable software approach. In other words, we began with a goal for how the material would perform. Our multiple iterations and shear tests confirmed that the material could achieve our structural goals, while the EPD validated that it would store more carbon than it emitted.
With their standard, machine-readable data format, EPDs could also become the basis for training future AI models. These models could help users select from an assortment of available materials based not only on environmental impact data, but also on more complex and fluid supply-chain information, local labor availability, holistic cost approaches, and human-centric aesthetics—among many other insightful considerations.
EPDs validate environmental impact data for materials. Others within industry can then use this material in their own net-zero projects, confident that the carbon data is accurate. Shown here is an example of a life cycle study that analyzed the carbon emitted during production, transportation, and use of the mycelium and FRP panel. This demonstrated a net-zero embodied carbon calculation (left) vs significant emissions from a typical panel (right).
Performance predictions
While Autodesk is exploring new ways to decarbonize building materials in the short term, it is evident that future software will need to adapt to the unique material conditions of local climates. Next-generation net-zero software tools will connect to databases of published EPDs to provide more precise environmental and performance data.
By having access to critical data during the earliest stages of a project, future designers will be better equipped to confidently adopt novel materials that respond to local conditions, ultimately improving project outcomes. The customer in Northern Europe can use Autodesk tools to design a cost-competitive, non-toxic passive house structure using locally sourced, thickened, prefabricated strawbale panels. The designer in West Africa can use load-bearing screens comprised of earth blocks and excavated site soil to build a naturally ventilated hospital–and in 25 years easily disassemble and reconfigure these screens to allow for future building renovations. And the design team in Chicago can develop a high-rise structure using a bacteria-fused, net-zero concrete alternative that is resilient in the face of climate change.
These disparate customers solving unique problems, each in their respective locations, are all united by data.
Get in touch
Have we piqued your interest? Get in touch if you’d like to learn more about Autodesk Research, our projects, people, and potential collaboration opportunities
Contact us